How To Cut Energy Bills On The Factory Floor
In the face of surging costs and in the absence of certainty, businesses across the globe are looking to reduce consumption and cut costs wherever possible. Businesses are struggling to cope with compounding costs and rising energy bills - that much is clear!
In the era of increased costs, acoustic imaging is offering manufacturers a crucial lifeline; it is helping energy-intensive industries to keep the lights on by managing operating costs and slashing maintenance expenses.
You’ve heard of ‘lossless sound’. Well, acoustic imaging takes that quite literally.
Detecting previously undetected air leaks can significantly reduce the costs.
For the UK (and much of the EU) the cost of energy has almost doubled from 34.0p/kWh in Feb 2023 verses Feb 2021 prices of 18.9p/kWh. That’s 179% higher!
In fact, gas prices have increased in 23 of the 24 EU Member States for which data is available, with the biggest jumps after the UK being seen in Estonia (+154%), Lithuania (+110%) and Bulgaria (+108%).
With large-scale industrial processes driven largely by compressors and vacuum pumps to operate machines and transport assets, the critical questions are:
- How can energy-intensive industries survive in this climate?
- How can manufacturers cut energy bills?
When it comes to condition monitoring, the answer is of course to look at your outgoings and real, tangible ways to cut expenditure on the factory floor. One way that is rapidly picking up traction among manufacturers across the breadth of the EU is acoustic imaging.
The average compressor system loses 80% of its energy to heat dissipation, meaning only 20% makes the transition into a usable output on the factory floor. Up to a third of this usable energy is lost to leaks. Energy you’re paying more and more to use!
Why Are Air Leaks So Expensive?
Let’s put a measurable scale on a problem that can vary substantially by application. To do this, operators must first explore exactly how much a leak can impact production costs. Take, for example, a compressed air leak from a small hole of just 1.5 millimetres on a network of compressed air systems at seven bars of pressure. Two years ago, with a price of £0.189 per kilowatt hour, that alone would have cost a company roughly £1,134 if you assume an operating time of 6000 hours per year.
With the energy situation worsening, costs may be three times higher than originally forecast. This can lead to a cost of up to £3,402 a year for failing to identify a single small hole in a vital production component. The scale of industrial manufacturing and scope for leaks to crop up unnoticed is staggering – yet such a comparatively small hole can compound into such a large problem.
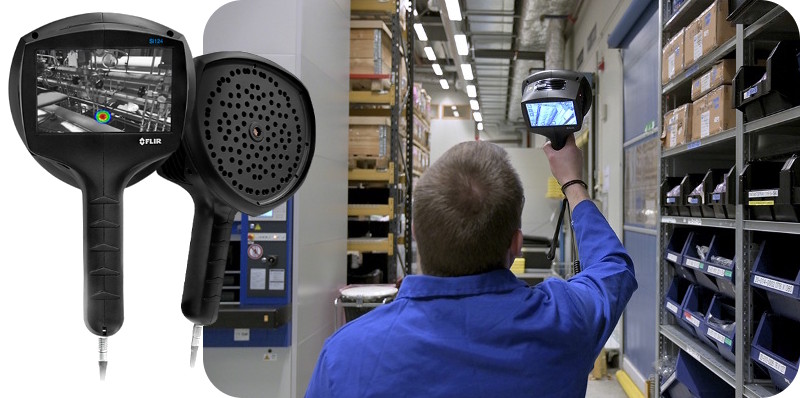
The FLIR Si124 Industrial Ultrasound Imaging Camera represents a new generation of acoustic imaging cameras, using a number of high-spec audible and ultrasound microphones to detect air leaks as they appear. It boasts an optimal bandwidth range of 2 - 65 kHz, which yields unmatched detection accuracy and identification down to even the smallest breach.
The technology within industrial ultrasound imaging cameras offers many benefits for operators. It's designed to identify, photograph or video the location of an air leak up to ten times faster (compared to traditional methods) - meaning minimal downtime for the facility and a prompt repair or replacement of the defective component. In addition to this, it also detects partial discharge, floating discharge and corona - helping to curb potentially life-threatening events, as well as general maintenance issues.
Operators benefit from considerably faster identification of problem parts and even have the capability to see the detected leak(s) as they appear.
They are able to see the detected leak(s) as they appear. This is because the sound is superimposed by functional AIs to render a visual depiction of where the leak is - as well as gauging its severity, including recommended actions to resolve.
In the case of the FLIR Si124, projective algorithms even estimate how much the leak will cost by evaluating the air lost in real-time and calculating the spend per kWh. Inspectors can review this information and all repairs are reflected in real-time, ensuring that inspectors have clear evidence needed to solve problems and justify any incurred repair costs across the production line.
If you’re a manufacturer struggling with the rising cost of energy, explore the new FLIR Si124 range now to radically improve inspections in your facility.