Crowcon WHITE PAPER: How A Compliance 4 Gas Unit Can Detect More Than 4 Gases
Ensuring the gas sensor you employ is fully optimised and reliable in the detection and accurate measurement of flammable gas and vapours is of the utmost importance regardless of the environment/workplace. This white paper will explore the ways in which conventional monitors can provide misleading indications of gas concentration if exposed to another gas or vapour from which they are calibrated. Here, we will provide guidance on how to avoid this in order to keep you and your workforce safe at all times.
“Conventional monitors can provide misleading indications of gas concentration if exposed to another gas or vapour from which they are calibrated.”
What Is A Compliance 4-Gas Monitor?
Gas sensors are primarily optimised for detecting specific gases or vapours through design or calibration. It is desirable that a toxic gas sensor, for example one detecting carbon monoxide or hydrogen sulphide, provides an accurate indication of the target gas concentration rather than a response to another interfering compound.
Personal safety monitors often combine a number of sensors for protecting the user against specific gas risks. A ‘Compliance 4-Gas monitor’ comprises sensors for measuring levels of carbon monoxide (CO) hydrogen sulphide (H2S), oxygen (O2) and flammable gases; normally methane (CH4). Many of the flammable gas sensors deployed in conventional monitors are optimised for detecting a specific gas or vapour through calibration, but will respond to many other compounds.
This is problematic and potentially dangerous as the gas concentration indicated by the sensor will not be accurate and may indicate a higher, or more dangerously a lower concentration of gas/vapour than is actually present.
With workers often potentially exposed to risks from multiple flammable gases and vapours within their work-place, it is incredibly important to ensure that they are protected through the implementation of an accurate and reliable sensor. Crowcon's new T4x Gas Detection Monitor with the ground-breaking MPSTM sensor is able to provide protection from CO, H2S, O2 risks with accurate measurement of multiple flammable gases and vapours utilising a basic methane calibration.
Detectors come in lots of different forms including fixed, portable or transportable and are designed to meet the needs of the user and environment whilst protecting the safety of those within it.
Fixed detectors, as the name suggests, are implemented as permanent fixtures within an environment to provide ongoing monitoring of plant and equipment. According to guidance from the Health and Safety Executive (HSE) these types of sensors are particularly helpful where there is the possibility of a leak into an enclosed or partially enclosed space which could lead to the accumulation of flammable gases.
Portable detectors normally come as a small, handheld device that can be used within smaller environments, confined spaces, to trace leaks or early warnings to the presence of flammable gas and vapour within hazardous areas.
Transportable detectors are not handheld, but they are easily moved from place to place to act as a monitor ‘stand-in’ whilst a fixed sensor is undergoing maintenance.
“Ensuring the gas sensor you employ is fully optimised and reliable in the detection and accurate measurement of flammable gas and vapours is of the utmost importance (regardless of the environment or workplace).”
“A 'Compliance 4-Gas Monitor' comprises sensors for measuring levels of carbon monoxide (CO) hydrogen sulphide (H2S), oxygen (O2) and flammable gases; normally methane (CH4).”
How Does The Molecular Property Spectrometry MPSTM Sensor Function?
The MPSTM sensor, which Crowcon’s new handheld T4x Gas Detection Monitor utilises, is a micro-electromechanical system (MEMS) transducer comprising an inert, micrometre-scale membrane with an embedded heater and thermometer. Crowcon have pioneered advanced property spectrometer sensor technology that detects and accurately identifies over 15 different flammable gases.
The sensor functions by rapidly heating and cooling, to measure changes in the thermal properties of the air due to the gases mixed within. Multiple measurements and environmental data are processed to classify the concentration of flammable gases or vapours present.
As can be seen on the chart below, the MPSTM sensor is able to measure the concentration of multiple flammable gases and vapours, including hydrogen, with a high degree of accuracy and without requiring re-calibration or the application of correction factors.
This technology offers a higher standard of flammable gas detection and is entirely focused on keeping people and premises safer than ever before, utilising more efficient and accurate testing.
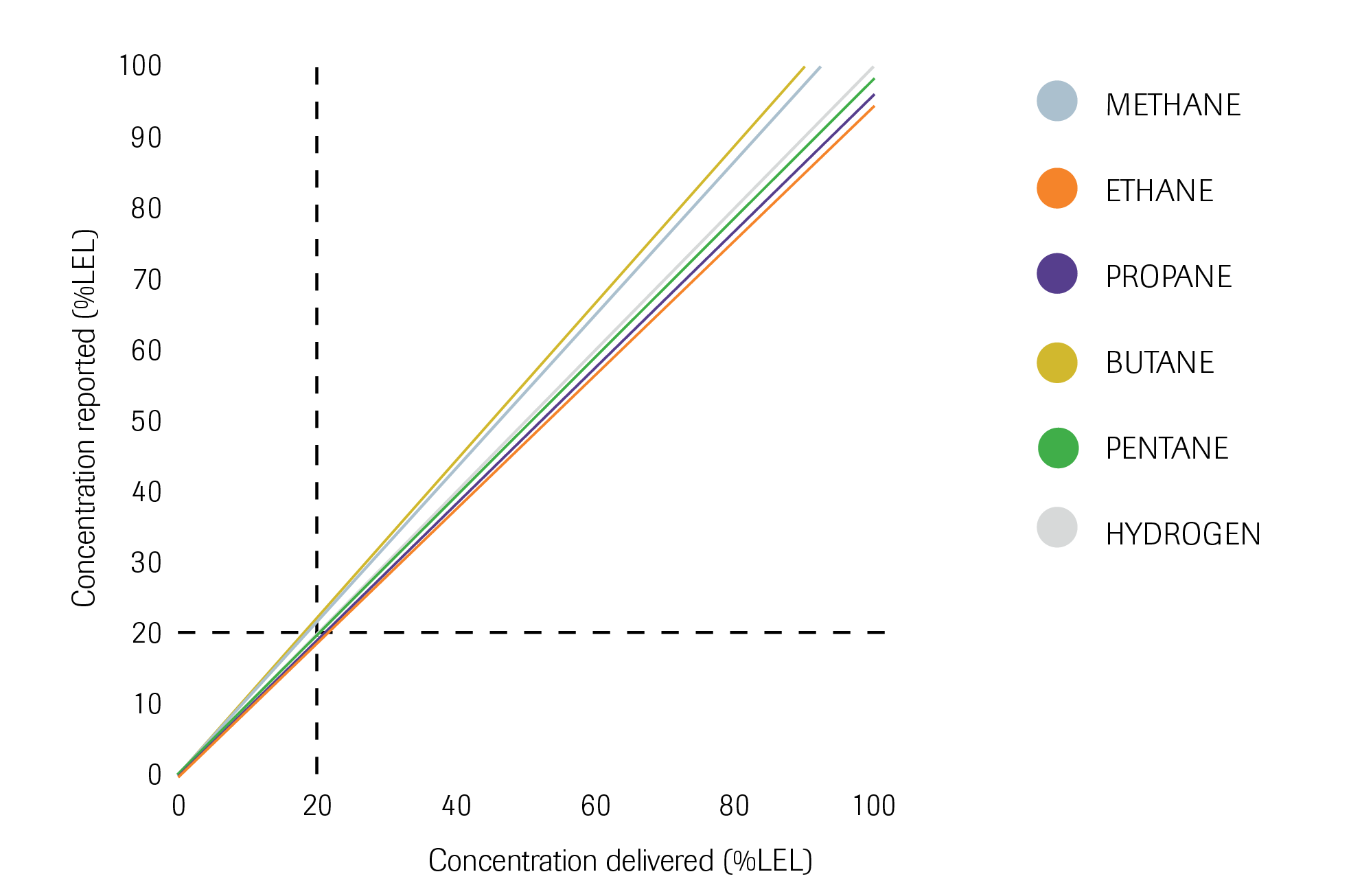
“Crowcon have pioneered advanced property spectrometer sensor technology that detects and accurately identifies over 15 different flammable gases.”
How Do IR (InfraRed) Sensors Function?
To put the MPSTM technology into context, it is important to explore other sensor technology and their functionalities to fully illustrate their pros and cons within a gas detection situation.
Gases and vapours are detected by measuring their absorption at particular frequencies of infrared energy which correspond to the resonance of the molecular bonds between dissimilar atoms. Most commonly encountered hydrocarbons, such as methane, propane and butane absorb IR energy in the range 3.3µ to 3.4µ. IR gas sensors are therefore filtered to measure IR absorption in this range.
The following table shows the response of an IR (infrared) sensor which is optimized or calibrated for methane detection when exposed to other compounds. As shown below, the sensor provides an accurate and linear measurement for methane, but massively over-responds to other common hydrocarbons such as propane or butane. This can lead to false alarms where only small or trace levels of gas or vapour leaks are present.
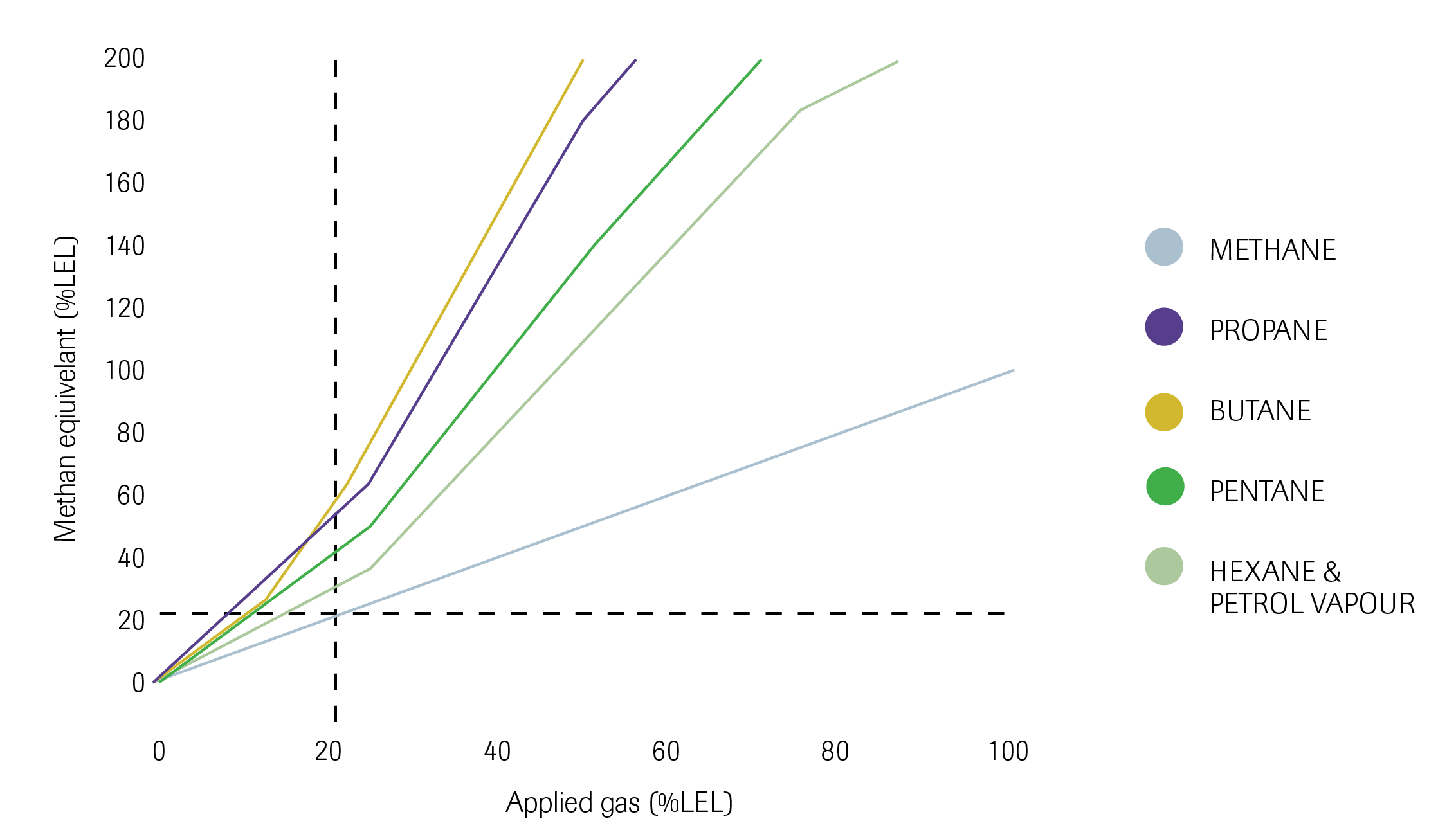
Speaking about the regularity of these alarms, the Health and Safety Executive say that these incidents can also be caused by fluctuance in the sensor output due to environmental changes. Environmental factors include ambient temperature, pressure or humidity. Therefore, it is important to be aware of the environmental factors that could affect readings within each gas detection context.
The HSE, in their publication "The selection and use of flammable gas detectors" also reiterate that false alarms can be triggered by sensitivity to other gases or vapours, as well as by sensor drift.
The HSE advice recommends that if false alarms are a problem you are encountering with the detector you are utilising you should take into account industry standards and recommendation, the lower explosion limit of the gas or vapour, the size of the potential leak and the time to reach a hazardous situation. They recommend regular checks to see if the area is occupied, to be aware of the time required to respond to the alarm, and the actions to be taken following the alarm, as well as to ensure a full comprehension of the toxicity of the gas or vapour in question.
Although regular checks for every sensor you are utilising are of course encouraged, it is important to be fully aware of the limitations of specific sensor types so that you can choose the best detectors that will keep you and your staff safe and secure.
Those using IR sensors that have been linearised and calibrated for detecting propane, for example, would find that they significantly under-respond if exposed to methane and indicate a %LEL concentration lower than is actually present. This obviously could present a safety risk and lead to inappropriate or inadequate responses from the user.
The IR sensor therefore is most suitable for use where the risk arises from a single, defined hydrocarbon gas or vapour, IR sensors are unable to detect Hydrogen.
How Do Pellistor Sensors Function?
The next sensor type to explore here is the pellistor sensors, also known as catalytic bead sensors. These consist of two matched platinum coils, each embedded in a bead of alumina. The detecting element is coated with a catalyst which promotes oxidation when in contact with flammable gases; the compensating element is treated so that catalytic oxidation does not occur. The compensating element is fitted to ensure that signals are not generated due to environmental effects, such as changes in ambient temperature or the gas flow rate. The two beads are placed in a circuit which causes them to heat to between 300-500˚C; a temperature where the reaction to flammable gases will occur. The instrument measures a small current offset in the circuit due to the increased resistance in the catalysed bead when gas is present. The signal change is then used to display the gas level and activate alarms. The pellistor responds to a huge range of compounds, however the response is variable to each and thus an accurate %LEL measurement can only be provided for the gas or vapour for which the sensor is calibrated. Some examples of the pellistor response factors are shown in the chart below to illustrate this variability.
Pellistors main disadvantage, specifically in the detection of hydrogen, is that they require oxygen which can make them unsuitable in some installations. Another challenge which is particularly relevant here is that unfortunately, pellistor sensors are vulnerable to permanent poisoning by silicones, lead, sulphurs or chlorinated compounds. If exposed to these compounds, a pellistor may fail to respond to flammable gas. This poisoning risk leaves workers unprotected and means that these sensors are not a fail-safe option for usage within your environment. A failed or inaccurate reading will not be detected unless a test gas is applied, commonly known as a bump test.
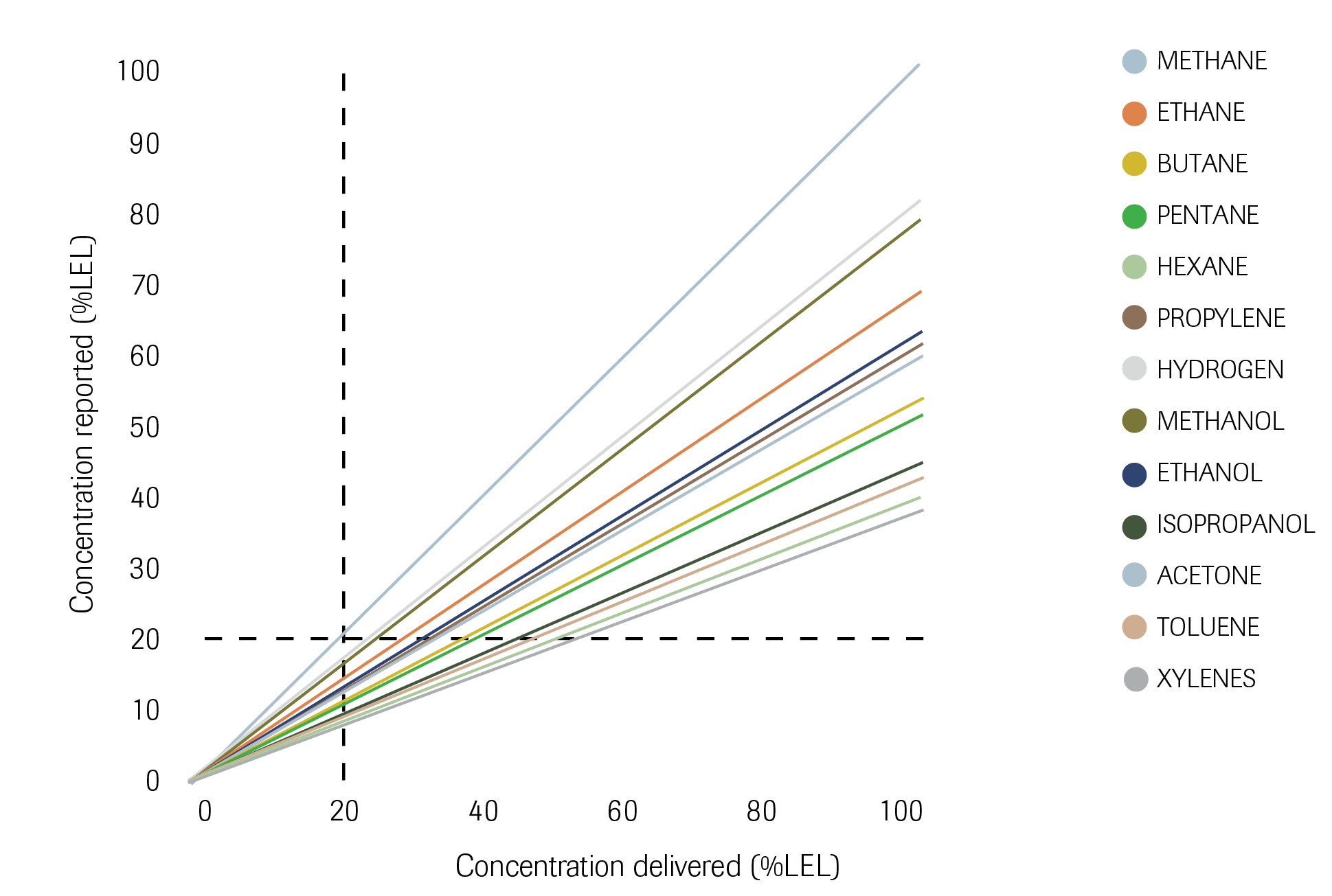
Crowcon T4 Portable 4-in-1 Gas Detector
To ensure ongoing reliability and accuracy the Crowcon T4x Gas Detector utilises the Molecular Property Spectrometry MPSTM Sensor functionality within its robust unit that provides a range of features to ensure safety.
The Crowcon T4 Gas Detector offers protection against the four common gas hazards: carbon monoxide, hydrogen sulphide, flammable gases and oxygen depletion, whilst the T4x Multi Gas Detector now comes with improved detection of pentane, hexane and other long chain hydrocarbons.
It comprises a large single button and easy-to-follow menu system to enable ease of use for those wearing gloves, who’ve undergone minimal training. Tough, yet portable, the T4x Gas Detector features an integrated rubber boot and an optional clip-on filter that can be easily removed and replaced when needed. These features allow the sensors to remain protected even within the dirtiest environments, to ensure they can remain reliable and accurate at all times.
Having been drop tested to 4 metre, as well as protected from water ingress through IP65 and IP67 certification, the sensor is robust in all senses of the word and crafted to remain operational and uninterrupted across a variety of demanding environments.
“The detector is not just reliable in terms of accurate detection and measurement of four gases, it is also dependable due to its battery life. It lasts for 18 hours.”
A unique benefit to the Crowcon T4x Gas Detector is that it ensures toxic gas exposure is calculated accurately throughout an entire shift, even if it is switched off momentarily, during a break or when travelling to another site. Normally, when most portable detectors are powered down, the algorithm that assesses TWA exposure is disrupted and assumes that it’s the end of the shift. So, when powering up, the detector begins again from zero, as if starting a new shift and ignores all previous measurements. The Crowcon T4x Gas Detector allows the user the option to include previous measurements from within the correct time frame.
The Crowcon T4x Gas Detector is not just reliable in terms of accurate detection and measurement of four gases, it is also dependable due to its battery life. It lasts for 18 hours and is useful for usage across multiple or longer shifts without requiring charging as regularly.
During usage the Crowcon T4x Gas Detector employs a handy ‘traffic light’ display offering constant visual assurance that it is operating soundly and conforming to the site bump test and calibration policy. The bright green and red Positive Safety LEDs are visible to all and, as a result, offer a quick, simple and comprehensive indication of the monitor’s status to both the user and others around them.
Best Practice For Portable Gas Detection
According to guidance from the Health and Safety Executive there are a number of best practices that need to be adhered to to ensure safe and efficient portable detection of flammable gases and vapours.
The HSE stresses the importance of proper training before operation. They advise that a robust training schedule should involve initially ensuring that the detector deployed is suitable for purpose and set correctly. Next the operator should undertake a test run to ensure accuracy in the readings and that the results are true.
As well as ensuring familiarity with, and an understanding of the device it is also necessary for operators to be fully au fait with their environment in terms of the hazards and properties of dangerous substances on site and which personal protective equipment is required. This means undertaking a thorough overview of PPE selection, by ensuring the correct fitting and use of respiratory protective equipment is undertaken utilising specialist expertise and training if and when required. You will also need to be aware of what action to take if the portable has detector alarms, and be able to effectively and efficiently implement the appropriate emergency procedures.
“Where you place the sensor should always comprehend the likely concentration gradients throughout the equipment and when there is the possibility of gas entering a confined space”
Active Or Passive Usage
HSE advises operators to be aware of the ways in which portable gas detectors can be utilised, including assessing whether the detector will be used actively or passively. Let’s explore these options for use here.
Active monitoring, as one would assume, involves the operator transporting the handheld detector during the monitoring process. This will mean monitoring the general area and the atmosphere within a confined space to search for any leaks from likely sources, such as drains or flange, during a shift.
Passive usage of a detector will see the operator placing the unit temporarily in one place to monitor the atmosphere. This temporary placement can be for a few hours or days depending on the needs of the environment and the current circumstances.
When determining the position of the portable detector for passive monitoring the operator can check the same points they would if they were positioning a fixed detector. Things points include:
- the process plant and equipment
- the type of sensor
- the properties and dispersion characteristics of the gas
- any relevant ventilation patterns
- location of staff
- whether multiple sensors are required
Where you place the sensor should always comprehend the likely concentration gradients throughout the equipment and when there is the possibility of gas entering a confined space, the sensors should be positioned close to ingress points. Whether you are using your detector actively or passively HSE stresses that the operator should power up the detector and note the readings in a gas-free area, before entering a hazardous area.
Delivering A Gold Standard Of Detection
In a bid to deliver a higher level of gas detection for your and your staff, Crowcon’s T4 portable 4-in-1 gas detector tackles the issue of sensor poisoning by resisting contamination through its specific design for today’s multi-gas environments. This gives your team peace of mind, as does the TrueLEL multi-gas measurement accuracy employed within the unit.
As the technology does not need calibration or scheduled maintenance during its five-year life span, it reduces interruptions to your day-to-day operations. With in-built self-monitoring and automatic problem reports you are secure in the knowledge of this reduced need for fleet maintenance. So, the larger your fleet, the greater the benefits.
The T4x and Gasman MPS is also ATEX Zone 0 approved which means operators can enter an area where an explosive gas atmosphere is present, for longer periods of time knowing that their unit will not ignite their environment.
With 50 years’ experience in the field, we are ideally placed to meet your needs, offer peace of mind to you and your team and offer advice and suggestions for effective and secure gas detection within your environment.
Choosing A Sensor You Can Be Sure Of
Crowcon’s T4x Compliance 4-Gas monitor fitted with the MPSTM sensor is able to protect workers from over 15 flammable gases and vapours, in addition to toxic H2S and CO gases and oxygen hazards.
The IR and Pellistor type sensors deployed in conventional monitors are effective at measuring a defined flammable gas or vapour, but are likely to provide misleading indications of gas concentration if exposed to another gas/vapour from which they are calibrated.
This means that choosing a sensor that you can be sure of is crucial when it comes to accurate measurement and detection of all gases or vapours that could pose a threat. The MPSTM sensor provides TrueLEL measurement of multiple flammable gases and vapours and is the ideal choice to keep you and your workforce safe and secure.
VIEW THE CROWCON T4 4-GAS MONITOR
VIEW THE CROWCON T4x MULTI-GAS MONITOR