The FLUKE ii910 Acoustic Camera, the innovative go-to tool for industry
If you've come from Control Automation and you like what you read below add code: Control Automation to your enquiry and receive a free demonstration at your facility... plus if you decide to purchase you can enjoy free calibration the following year!
If you've come to this web resource you'll want to know how the FLUKE ii910 Acoustic Camera can help you? So lets get started!
The FLUKE ii910 has been built to detect:
✓ Compressed air, gas and vacuum leaks
✓ Electrical discharge
✓ Potential bearing failures
The ii910 will recognise high frequency sounds associated with leaks/failures; it's 64 micro-electronic surface-mount microphones capture sound waves emanating from an object. An innovative go-to tool for industry. Don't get left behind because it is a solution for the entire maintenance team; applicable to any maintenance strategy (preventive or reactive).
☺️ No more time consuming tasks
☺️ No need to shut-down
☺️ No need to be close to the object in question to find the leaks
☺️ No more climbing ladders or crawling around equipment
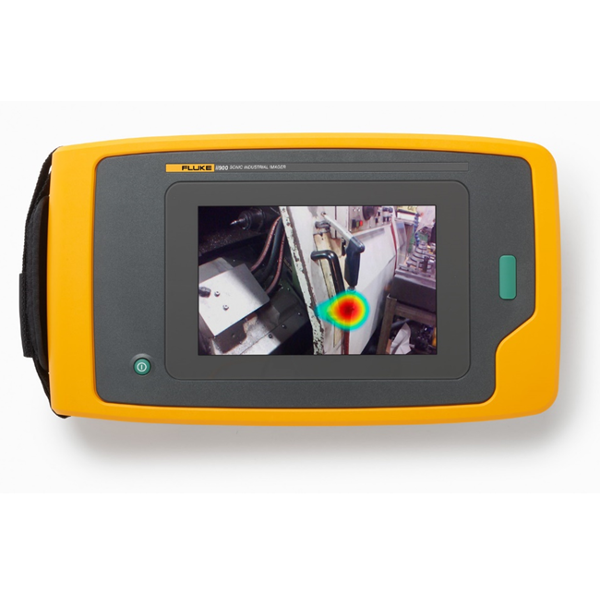
FLUKE ii910 can help protect your company from the above potential issues:
- Find compressor system leaks (typically ranging from 30 to 60kHz)
- Research has shown a plant with compressed air can waste up to 30% of its total compressed air production capacity through leaks. Find the leaks, reduce waste, save money
- Electrical leaks / Partial discharges (typically ranging from 20 to 110 kHz)
- Keep your assets in good working order, avoid unplanned downtime and keep your staff safe
- And of course identification of potential bearing failures
- MecQ technology offers pre-defined and customisable frequency bands. The sub-modes allow filtering and trending of dB level data at any frequency band perfect for picking up on impending bearing issues and mechanical failure
The FLUKE ii910 Acoustic Camera is easy-to-use
With short demonstration carried out by Acutest you are ready to find those problems which impact your bottom line.
This device is key for:
✓ Visual localisation of leaks
✓ Quick detection from a distance
✓ Time-saving benefits
✓ Reliable operation in noisy environment
✓ Improved process control, less recycling
✓ Increased efficiency
✓ Leak quantification
✓ Easy documentation
✓ Cost reduction
So what if you only want to detect compressed air, gas and vacuum leaks?
And you're not interested in the other two applications!
The solution is the FLUKE ii900 however the FLUKE ii910 has a greater detection range:
- ii900: Up to 70 meters (230 feet)*
- ii910: Up to 120 meters (393 feet)*
Reduce costs: Research has shown a plant with compressed air can waste up to 30% of its total compressed air production capacity through leaks. Find the leaks, reduce waste, save money.
Build maintenance efficiency: Enable your maintenance team to easily standardise leak detection audits and fix leaks on the go, and simplify reporting leaks in your workflow system
Eliminate more unplanned downtime: Unplanned downtime costs!
Optimise asset performance: Build asset-specific historical data for preventive maintenance planning
Generate reports: Generate reports and analyse losses to meet ISO50001 energy management requirements
Improve safety around hazardous gases: Propane, methane, fuel, acetone, ethanol, and benzene are among the hazardous gases that can be found within commercial and residential areas. Leaks of some gases can result in an explosion
Quickly pinpoint: Find those invisible and difficult to-access leaks to improve safety
Safeguard production quality: A drop in system pressure can make air tools function less efficiently and adversely affect production quality. Leaks can cause system pressure drops and shorten the life of system equipment, including the compressor
CO2 emission estimator: With the new CO2 emission estimator (weight) feature, part of the FLUKE Online LeakQ reporting tool, you can quantify the impact of each individual and total number of leak(s)
Quantify CO2 emissions impact: Quantify the environmental and financial value of compressed are leaks. Drastically reduce your energy use and carbon footprint which helps ensure cleaner air, water, and food for our generation and for generations yet to come
Improve uptime, save energy costs, and reduce your carbon footprint; anyone can identify leaks and where a compressed air leak might exist, and the size of the leak is.
▶ Video: FLUKE ii900/ii910 - scan large areas quickly, even from a distance!
If you are interested in finding compressed air leaks at greater distances, electrical discharge and bearing issues then the FLUKE ii910 is the perfect fit!
Lets see what extras you get...
All three applications are covered with the ii910 plus detect from further away (120 meters / 393 feet)*
Detect partial discharge (PD Detection): Whether you are inspecting insulators, transformers, switchgears or high voltage powerlines you need to be sure that you spot a problem quickly and early.
Unchecked partial discharge: increases blackouts, fires, explosions, or death from arc flashes. In addition to the danger that partial discharge poses to human lives and the environment, there is a significant monetary risk of downtime.
Detect potential bearing issues: MecQ is a powerful solution that can significantly reduce unplanned downtime by locating potential issues in conveyor systems so they can be addressed on your maintenance schedule. See potential issues before they cause unplanned downtime with quick and easy visual detection.
Bearing efficiency: reduce the risk of unplanned downtime. Reduce mean time to repair KPI (be ahead of the problem for in-time ordering of spare parts) and there is no need for close proximity (contact) measurement, avoiding hazardous situations for your staff
Deploy with Ease / Boost Efficiency / Maximise Uptime / Ensure Team Safety / Reduce Costs
So which industries would benefit having the FLUKE ii910/ii900 in their test and measurement kit?
- Processing plants (eg chemical)
- Food and beverage facilities
- Pharmaceutical plants
- Automotive
- Manufacturing (eg cement, aerospace, glass, metal, rubber and plastics)
- Pulp and paper mills
- Mining
- Utilities
- Oil and gas
ARRANGE A FLUKE ii900 SERIES DEMO [FREE]
REQUEST OUR BEST PRICE