🔋 Why Battery Failures Matter – And How Megger Industrial Battery Testers Can Help
Today, we rely more than ever on batteries to keep our systems running. From data centers to hospitals and renewable energy, battery backups are critical. But when batteries fail, the consequences can be serious—and expensive. That’s why using the right tools, like industrial battery testers and megger battery testers, is essential to keep things working smoothly.
Replacing batteries is costly, and downtime can cost even more. Regular testing helps catch problems early. There are two main ways to test batteries:
- Impedance testing – Done while the battery is online. It helps spot weak cells before they fail. Many industrial battery testers and megger battery testers are built for this.
- Battery discharge testing – Done offline to show how the battery performs under load. It gives a real-world picture of how the system would behave in an outage.
In floating battery systems, earth faults are a concern. Tools like ground fault tracers—often included with megger battery testers—help track down problems quickly.
📈 The Growing Need for Battery Testing
Batteries are no longer optional—they’re a core part of modern life. One hour of downtime in a data center can cost over £80,0000. To avoid this, regular checks with Megger Industrial Battery Testers are key.
4 key parts of this BLOG POST:
- Learn why batteries fail, to help you stay one step ahead
- Discover common battery failures and how the right testers can help prevent them
- Look at battery testing schedules
- Discover the Megger portfolio of industrial battery testers
🔋 Common Lead-Acid Battery Failures
- Positive Grid Corrosion – Caused by heat and overcharging. Megger Industrial battery testers catch these issues early.
- Sulphation – Happens when batteries sit unused. Megger battery testers can detect it before lasting damage sets in.
- Internal Shorts – Can happen suddenly. Regular testing with Megger battery testers helps find them early.
- Dry-Out (in VRLA batteries) – Loss of electrolyte raises resistance. Industrial battery testers show performance drops.
- Thermal Runaway – Overheating danger. Megger battery testers spot early warning signs like rising temperatures.
🔋 Common Lithium-Ion Battery Failures
- SEI Layer Build-Up – Causes heat and voltage issues. Megger Industrial battery testers track these changes.
- Lithium Plating – A safety hazard. These types of testers help catch it early.
- Uneven Ageing – Different parts wear out unevenly. Industrial battery testers keep systems balanced.
- BMS Failures – Can allow overcharging or overheating. These testers offer an extra layer of protection.
- Inter-Cell Connection Issues – Cause heat and resistance. Megger Industrial battery testers detect them quickly.
🛡️ The Best Way to Prevent Battery Problems
Most battery failures don’t happen without warning. Regular testing with Megger Industrial Battery Testers can catch issues early, before they cause trouble.
Benefits of regular testing include:
- Better reliability
- Longer battery life
- Improved safety
- Lower overall costs
HOW BATTERIES GO BAD: UNPACKING FAILURE MODES
In this Megger guide they cover: 1. Lead-acid and lithium-ion failure modes 2. Grid corrosion and sulphation 3. Thermal runaway and lithium plating 4. BMS and connections
Don’t let battery failures jeopardise your operations.
Industrial Battery Testing Schedule
Standard Battery Testing Requirements Summary
The tables below summarise the testing requirements and schedules from the following standards:
- IEEE Std 450-2010: IEEE Recommended Practice for Maintenance, Testing, and Replacement of Vented Lead-Acid Batteries for Stationary Applications
- IEEE Std 1188-2005: IEEE Recommended Practice for Maintenance, Testing, and Replacement of Valve-Regulated Lead- Acid (VRLA) Batteries for Stationary Applications
- ANSI/NETA MTS-2015
- NERC Standard PRC-005-6: Protection System, Automatic Reclosing, and Sudden Pressure Relaying Maintenance.
I = Indicates recommendations by IEEE Standards
N = Indicates recommendations by NETA Standard for Maintenance Testing Specifications
P = Indicates NERC PRC-005-6 requirements
LEAD ACID BATTERY - MONTHLY
LEAD ACID |
Monthly |
ACTIVITY |
VLA |
VRLA |
Float voltage measured at the battery terminals |
I |
|
I |
|
General appearance and cleanliness of the whole installation |
I |
N |
I |
N |
Charger output current and voltage |
I |
|
I |
|
Crack in cells (evidence of electrolyte leakage) |
I |
|
I |
|
Evidence of corrosion at terminals, connectors, racks or cabinets |
I |
N |
I |
N |
Ambient temperature and ventilation |
I |
N |
I |
N |
Pilot cells (If used) voltage and electrolyte temperature |
I |
|
|
|
Battery float charging current or pilot cell specific gravity |
I |
|
|
|
Unintentional battery grounds |
I |
N |
|
N |
Electrolyte levels |
I |
N |
|
|
Cell-to-cell and terminal connection resistance |
|
N6 |
|
N6 |
Structural Integrity of the battery rack |
|
N |
|
N |
Verify tightness of accessible bolted electrical connections5 |
|
N6 |
|
N6 |
Perform a thermographic survey under load7 |
|
N6 |
|
N6 |
Verify presence of flame arresters |
|
N |
|
|
Verify existence of suitable eyewash equipment |
|
N |
|
N |
LEAD ACID BATTERY - QUARTERLY/TRI-ANNUAL
LEAD ACID |
Quarterly/Tri-annual* |
ACTIVITY |
VLA |
VRLA |
Float voltage measured at the battery terminals |
I |
P |
I |
|
General appearance and cleanliness of the whole installation |
I |
|
I |
|
Charger output current and voltage |
I |
|
I |
P |
Crack in cells (evidence of electrolyte leakage) |
I |
|
I |
|
Evidence of corrosion at terminals, connectors, racks or cabinets |
I |
|
I |
|
Ambient temperature and ventilation |
I |
|
I |
|
Pilot cells (If used) voltage and electrolyte temperature |
I |
|
|
|
Battery float charging current or pilot cell specific gravity |
I |
|
|
|
Unintentional battery grounds |
I |
P |
|
P |
Electrolyte levels |
I |
P |
|
|
Voltage of each cell |
I |
|
I |
|
Specific Gravity of 10% of the cells of the battery |
I2 |
|
|
|
Temperature of at least 10% of cells |
I |
|
|
|
Temperature of the negative terminal of each cell |
|
|
I |
|
Cell/unit internal ohmic values |
|
|
I |
P10 |
LEAD ACID BATTERY - YEARLY / 18 MONTHS
LEAD ACID |
Yearly/18-months* |
Activity |
VLA |
VRLA1 |
Float voltage measured at the battery terminals |
I |
N |
P |
I |
N |
P1 |
General appearance and cleanliness of the whole installation |
I |
|
|
I |
|
|
Charger output current and voltage |
I |
|
|
I |
|
|
Crack in cells (evidence of electrolyte leakage) |
I |
|
|
I |
|
|
Evidence of corrosion at terminals, connectors, racks or cabinets |
I |
|
|
I |
|
|
Ambient temperature and ventilation |
I |
|
|
I |
|
|
Pilot cells (If used) voltage and electrolyte temperature |
I |
|
|
|
|
|
Battery float charging current or pilot cell specific gravity |
I |
|
|
|
|
|
Unintentional battery grounds |
I |
|
|
|
|
|
Electrolyte levels |
I |
|
|
|
|
|
Voltage of each cell |
I |
N |
|
|
N |
|
Specific Gravity of 10% of the cells of the battery |
I |
|
|
|
|
|
Temperature of at least 10% of cells |
I |
|
|
|
|
|
Temperature of the negative terminal of each cell |
|
|
|
I |
N |
|
Specific Gravity of all cells |
I2 |
|
|
|
|
|
Cell condition |
I |
|
P |
|
|
|
Cell/unit internal ohmic values |
|
N |
P4 |
I |
N |
P |
Cell-to-cell and terminal connection resistance |
I |
N |
P3 |
I |
N |
P |
Structural Integrity of the battery rack |
I |
|
P |
|
|
P |
AC ripple current and/or voltage imposed on the battery |
|
|
|
I |
|
|
Performance or modified performance capacity test of entire bank |
I8 |
N8 |
P4 |
I9 |
N9 |
P10 |
Verify equalising voltage setting is in accordance to battery’s manufacturer recommendation |
|
N |
|
|
N |
|
Verify all charger functions and alarms |
|
N |
|
|
N |
|
NiCad BATTERY - QUARTERLY/TRI-ANNUAL
NiCad |
Quarterly/Tri-annual* |
ACTIVITY |
|
|
Float voltage measured at the battery terminals |
I |
|
General appearance and cleanliness of the whole installation |
I |
|
Charger output and voltage |
I |
|
Electrolyte levels |
I |
P |
Unintentional battery grounds |
|
P |
Crack in cells (evidence of electrolyte leakage) |
I |
|
Evidence of corrosion at terminals, connectors, racks or cabinets |
I |
|
Ambient temperature and ventilation |
I |
|
Pilot cells (If used) voltage and electrolyte temperature |
I |
|
Verify Station DC supply voltage |
|
P |
NiCad BATTERY - SEMI-ANNUALLY
NiCad |
Semi-annually |
ACTIVITY |
|
Float voltage measured at the battery terminals |
I |
General appearance and cleanliness of the whole installation |
I |
Charger output and voltage |
I |
Electrolyte levels |
I |
Crack in cells (evidence of electrolyte leakage) |
I |
Evidence of corrosion at terminals, connectors, racks or cabinets |
I |
Ambient temperature and ventilation |
I |
Pilot cells (If used) voltage and electrolyte temperature |
I |
Voltage of each cell |
I |
NiCad BATTERY - YEARLY / 18 MONTHS
NiCad |
Yearly/18 months* |
ACTIVITY |
|
|
|
Float voltage measured at the battery terminals |
I |
N |
|
General appearance and cleanliness of the whole installation |
I |
N |
P |
Charger output and voltage |
I |
|
P |
Charger float and equalising voltage levels. Adjust to manufacturer’s recommended settings. |
|
N |
P |
Verify all charger functions and alarms |
|
N |
|
Electrolyte levels |
I |
|
|
Crack in cells (evidence of electrolyte leakage) |
I |
|
|
Evidence of corrosion at terminals, connectors, racks or cabinets |
I |
|
|
Ambient temperature and ventilation |
I |
N |
|
Pilot cells (If used) voltage and electrolyte temperature |
I |
N |
|
Voltage of each cell |
I |
N5 |
|
Intercell connection torque |
I |
|
|
Condition and resistance of cable connections |
I |
N2 |
P |
Verify tightness of accessible bolted electrical connections by calibrated torque-wrench3 |
|
N2 |
|
Perform thermographic survey4 |
|
N2 |
|
Structural Integrity of the battery rack |
I |
N |
P |
Verify existence of suitable eyewash equipment |
|
N |
|
Verify application of an oxide inhibitor on battery terminal connections |
|
N |
|
Perform internal ohmic measurements |
|
N |
|
Perform load test |
|
N6 |
|
Measure battery system voltage from positive-to-ground and negative-to-ground |
|
N |
|
Performance or modified performance capacity test of entire bank |
I7 |
N6 |
|
NiCad BATTERY - 6 YEARS
NiCad |
6 Years |
ACTIVITY |
|
Performance or modified performance capacity test of entire bank |
P |
(correct as of MAY 2025 - to see the Megger Battery Testing document click here)
Final Thoughts
Battery problems don’t have to catch you by surprise. Whether it's slow damage like sulphation or fast failures like thermal runaway, most issues are avoidable. With the help of industrial battery testers and megger battery testers, you can spot problems early and take action before it’s too late.
Discover Megger Battery Testers – engineered to maximise performance and reliability. See why professionals choose Megger
Megger BVM Monitors provide easy and economical expandability to meet testing requirements of small-to-large battery bank systems. Automates battery voltage measurement during capacity tests.
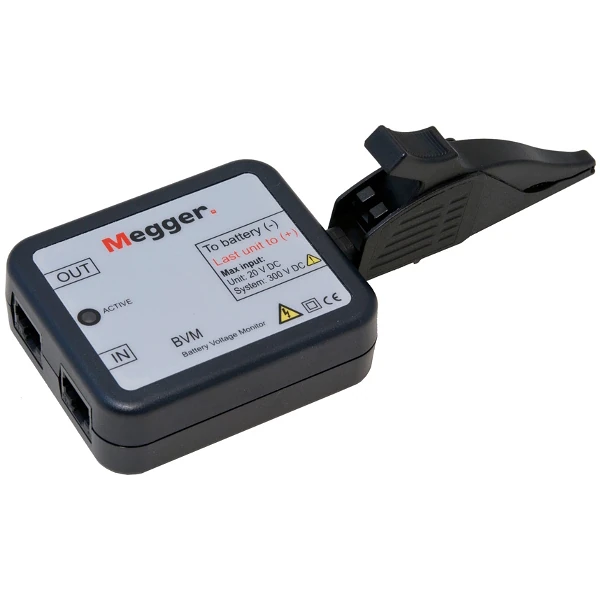
Megger BITE 5 Battery Tester (lead acid, NiCD, & lithium-ion). Measure, record and trend battery voltage, impedance and temperature. An all-in-one battery testing device.
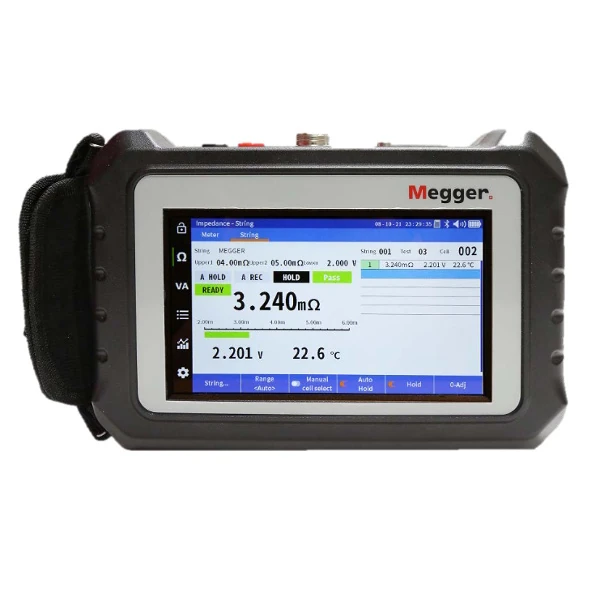
Megger TXL890 Extra Load Units for TORKEL Battery Test Systems. TXL extra load units plus the TORKEL together form a system which can discharge batteries with currents of up to several kA.
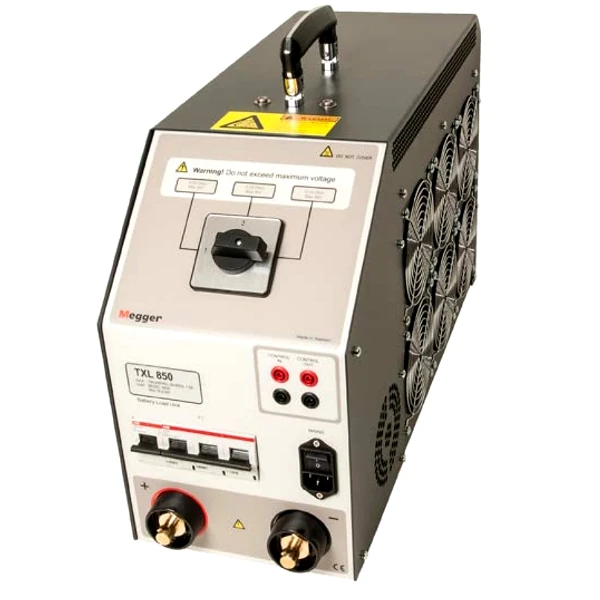
Megger TORKEL 910 Battery Load Tester performs load tests or discharge tests to determine a battery systems actual capacity. For use in HV substations & industrial environments.
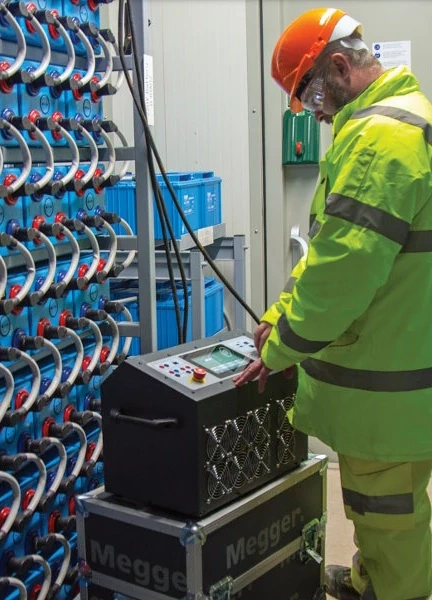