Power Quality Solutions for the Water and Wastewater Industry (and other tools)
Electrical Engineer's Toolbox within the Water Industry
|
Process Engineer's Toolbox within the Water Industry
|
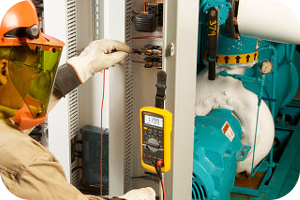
|
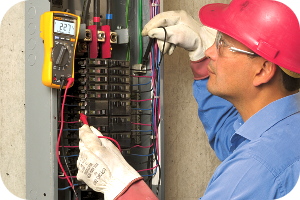
|
87V Digital Multimeter (True RMS)
|
117 Digital Multimeter (Non-Contact Voltage Detection) |
Safe, Rugged and Accurate Digital Multimeter |
Integrated non-contact digital multimeter |
Water Industry Electrical Engineer's Useful Features: |
Water Industry Process Engineer's Useful Features: |
- Safer and rugged: Safety rated CAT III 1000 V, CAT IV 600 V
- Accurate: Measure current, voltage and frequency on complex variable frequency drive (VFD) signals
- This electrical Multimeter correctly measure pulse-width modulated motor drive signals
- Save time: The 87V Multimeter includes a built-in thermometer and temperature probe
- True-RMS AC voltage and current for measuring non-linear signals
|
- Non-contact voltage detection
- AutoVolt automatic AC/DC voltage selection
- Prevent false readings caused by ghost voltage
|
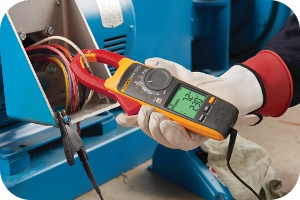 |
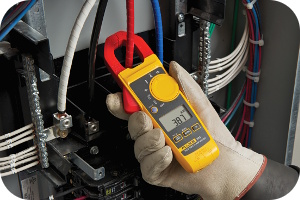 |
378FC Clamp Meter |
325 Clamp Meter |
Inc. iFlex flexible current probe & TPAK magnetic hanging accessory |
Compact form making measurements easily in cable compartments |
Water Industry Electrical Engineer's Useful Features: |
Water Industry Process Engineer's Useful Features: |
- 1000A AC/DC TRMS non-contact voltage wireless clamp
- Measure voltage and current with your clamp jaw
- Faster, safer testing - all without touching a live wire - using FieldSense technology
- Power quality indicator shows whether equipment or power line is faulty
- Complete 3-phase voltage and current tests in 3 quick steps
|
- True-rms AC/DC current, voltage, temperature, frequency
- Clamp meter, test leads, K-type thermocouple and soft case
- Versatile tool performs most front-line measurement tasks
|
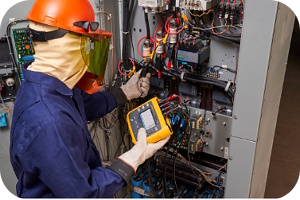 |
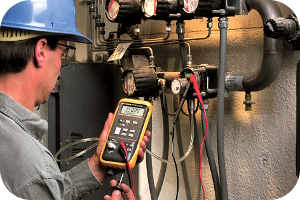 |
1738 Power Quality Logger |
718 Process Calibrator
|
Automatically capture & log over 500 PQ parameters |
Protect the pump from damage. Service the pump without disassembly |
Water Industry Electrical Engineer's Useful Features: |
Water Industry Process Engineer's Useful Features: |
- Versatile, 3-phase power logger
- Conducts energy, load and power quality studies
- Automatically capture and log: voltage, current, power, harmonics and associated power quality values
- Capture: dips, swells and inrush currents with event waveform snapshots and high-resolution RMS profiles
- Convenient instrument powering directly from the measured circuit
- Download and analyse every detail of energy consumption and power quality state of health with our automated reporting
View Power Quality water industry application in more detail.
|
- Pressure source and mA measurement to calibrate pressure devices
- Built-in pump for sourcing pressure to 300 PSI
- Easy-to-clean, field-serviceable, integrated pressure pump
- Built-in switch test for calibrating pressure switches
- Extend pressure capabilities by using FLUKE 750P pressure modules
|
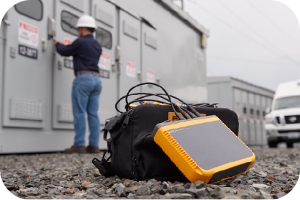 |
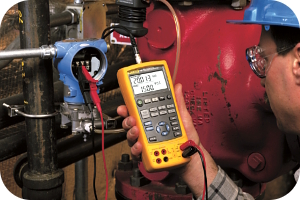 |
1748 Power Quality Logger |
725 Process Calibrator |
Reliable data for analysis, system planning & demand management |
Precise & powerful, yet easy-to-use field calibrator |
Water Industry Electrical Engineer's Useful Features: |
Water Industry Process Engineer's Useful Features: |
- Troubleshoot, quantify energy usage and analyse power distribution systems in a fast, easy and safe way
- Connectivity: WIFI (or ethernet) connected to view data directly in the field
- IP65 Rated Casing making unit suitable for outdoor logging sessions
- Transient detection
View Power Quality water industry application in more detail.
|
- Calibration of both temperature and pressure transmitters
- Measure/source/simulate mA loop parameters
- Measure and source mA, Volts DC, frequency, and resistance
- Built-in 24 V loop power supply
- Store and recall frequently used calibration set ups
|
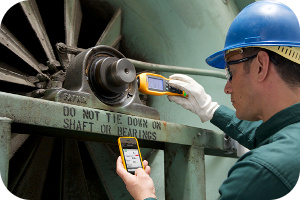 |
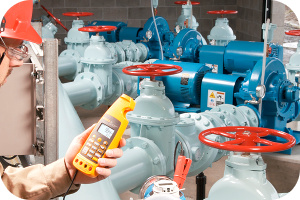 |
805 FC vibration Meter |
772 Process Clamp & 773 Process Clamp |
Make go or no-go maintenance decisions with confidence |
Save time & money measuring output signals without shut down |
Water Industry Electrical Engineer's Useful Features: |
Water Industry Process Engineer's Useful Features: |
- Reliable, repeatable, accurate device for checking bearings and overall vibration
- Features innovative sensor design that minimises measurement variations caused by device angle or contact pressure
- Provides consistent data quality at both low and high frequency ranges
- Offers four-level severity scale to assess urgency of problems and bearing condition
|
- Loop meter that measures 4 to 20 mA signals without breaking the loop
- Features best in class 0.2% accuracy
- Simultaneously measure mA in-circuit with 24 V loop power for powering and testing transmitters
- Delivers 0.01 mA resolution and sensitivity
- Measures mA signals for PLC and control system analogue I/O
Extra for the 773 Process Clamp:
- Source DC Voltage 0-10V
- Measure DC Voltage 0-30V
- Scaled mA Output to a mA Input
- mA in/out to simultaneously measure the mA signal with the Clamp and source mA signal
|
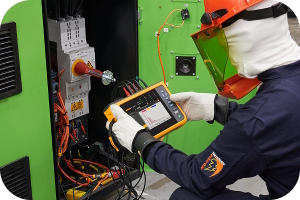 |
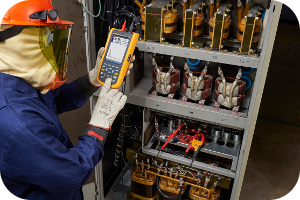 |
1773 Series Power Quality Analyser (1775 & 1777) |
125B ScopeMeter |
Engineered to be the faster, easier way to perform power quality studies |
For industrial electrical & electro-mechanical troubleshooting |
Water Industry Electrical Engineer's Useful Features: |
Water Industry Process Engineer's Useful Features: |
- Automatically measure power and power quality parameters
- At-a-glance power quality health for faster troubleshooting
- Easily view V/A/Hz, power, dips, swells, and harmonics data
- Capture high-speed transients up to 8 kV (1775 & 1777 only)
- Power directly from measurement circuit without a line cord
View Power Quality water industry application in more detail
|
- Dual-input digital oscilloscope and Multimeter in a ScopeMeter test tool
- Available with a 40 MHz oscilloscope bandwidth
- Features Connect-and-View trigger simplicity for hands-off operation
- Includes IntellaSet technology to automatically and intelligently adjust numerical readout based on measured signal
- Provides a dual-input waveform and meter reading recorder for trending data over extended periods
|
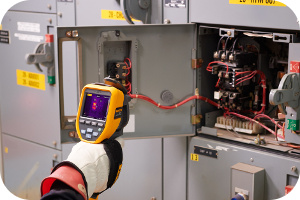 |
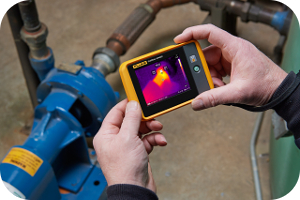 |
TiS75+ Thermal Imaging Camera |
PTi120 Thermal Imager |
Feature-rich camera helps you tackle almost anything you’ll face in the field! |
Designed for quick temperature scans minimise downtime |
Water Industry Electrical Engineer's Useful Features: |
Water Industry Process Engineer's Useful Features: |
- Fully radiometric thermal imager gives you measurement data to the pixel with 384 x 288 infrared resolution
- Asset Tagging
- Touchscreen IR Fusion
- IS3 and AVI video recording
- Measure from -20°C up to +550 °C
- Dew-point calculation
|
- Automatically organise & file thermal images with FLUKE Connect Asset Tagging
- Fully radiometric thermal imager gives you measurement data to the pixel with 120 x 90 infrared resolution (10,800 pixels)
- 3.5" LCD touchscreen display for easy troubleshooting
- -20 °C to +400 °C temperature measurement range
- Six colour palettes
- Can withstand drop up to 1 meter
- IP 54 enclosure rating
|
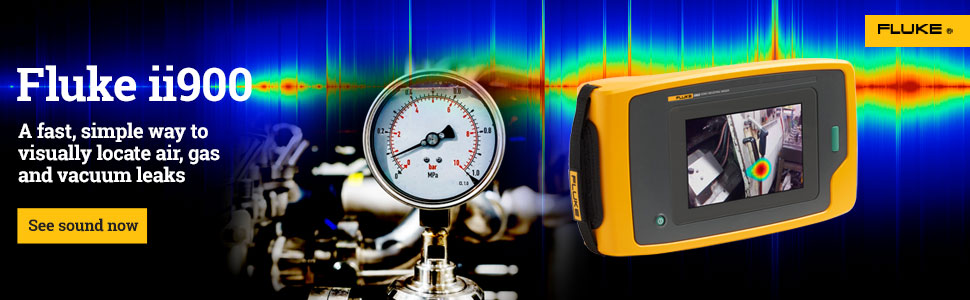
FLUKE ii900 Sonic Industrial Imager
Quickly & simply detects compressed air, steam, gas & vacuum leaks
Water Industry Electrical Engineer's Useful Features:
- Do more with the same air compressors – delay the capital expense of purchasing an additional compressor
- Ensure proper air pressure to your pneumatic equipment
- Lower utility costs
- Reduce leak detection time
- Improve reliability in your production line
- LeakQ Report Generator
Clean power delivers clean water
This story features a regional wastewater treatment plant on the shores of Puget Sound, Washington. An award-winning facility serving six cities, the plant processes an average of 21.1 million gallons of wastewater daily, with a daily capacity of up to 28.7 million gallons.
Most water treatment facilities use the same basic processes, but this one has been continuously updated since it opened in 1984, including high-intensity UV light and soon, a new Class "A" biosolids drying facility.
In this particular case, maintenance electrical specialist Mark Newport was in the process of installing new electronic power factor correction units at multiple motor control centres (MCCs) to improve power quality, protect equipment and reduce costs. However, since corrective measures can often introduce new power quality problems into the system, he used a handheld FLUKE 434 three-phase Power Quality Analyser to make sure their efforts were successful*.
*Since this case study was written the FLUKE 434 has been replaced by the FLUKE 1770 Series / 1738 & 1748 three-Phase Power Quality Analysers.
System Details
The treatment plant relies on hundreds of motors, some as large as 500 hp. A SCADA control system is interfaced to the MCCs, as well as valves, actuators, sensors, and power monitors. It also allows instant visibility into the system at numerous stations.
If the plant went down for any reason, such as a regional power outage, sewage would continue to flow through the plant and though the sedimentation tanks, but it would be discharged into Puget Sound without full treatment.
To prevent this from ever happening, the plant electrical system has several levels of redundancy. It's served by dual utility feeds from two substations. Generally the load is shared between the two feeds, but either feed can handle the whole facility through a tiebreaker system. A 1.25 MW generator on an automatic transfer switch can take over within 8 seconds, if both utility feeds fail. Small, single-phase Uninterrupted Power Supplies (UPS) maintain the elements of the redundant control system while the generator starts and synchs.
Power Correction
The power correction systems were being installed primarily to correct power factor. The same conductors were used to feed both adjustable-speed motor drives (ASDs) and across the line motor starters. The ASDs are non-linear loads and draw harmonic currents, especially at the fifth harmonic. Power factor capacitors present a lower impedance to higher frequencies, than to the 60 Hz fundamental. So a system with harmonic currents can cause overcurrent in correction capacitors. Maintenance staff at the plant realised this and decided to use a semiconductor-based device instead.
The device they connected to each MCC continuously monitors a circuit's power factor. It generates leading reactive power (VAR's) to counteract the inductive, lagging VAR's from the motors. It can respond instantly to load changes. In addition, it looks for any harmonic current and generates an inverted signal to cancel it. So, to any upstream devices it appears as if the MCC is a resistive load.
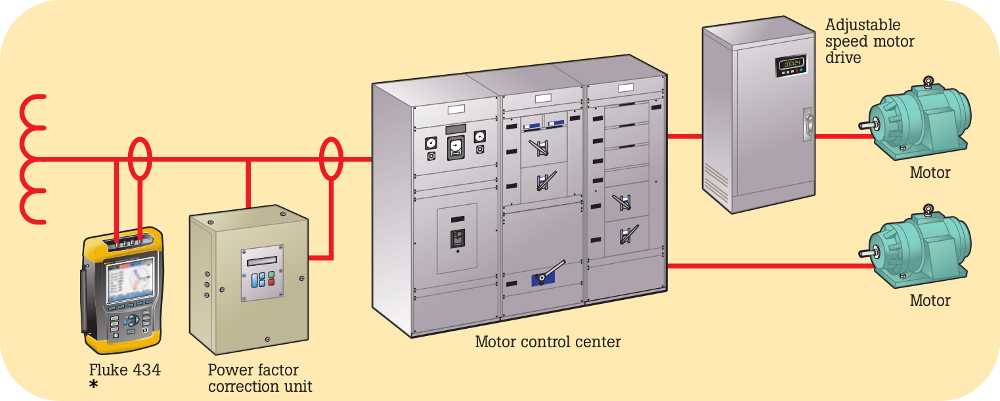
Figure 1. System connections
*Since this case study was written the FLUKE 434 has been replaced by the FLUKE 1770 Series / 1738 & 1748 three-Phase Power Quality Analysers.
What is Power Factor? Why Does it Matter?
Power factor is a measurement that compares the real power (watts) being consumed to the apparent power (Volts-Amps) of the load. A purely resistive load would have a power factor of 1.0.
What does it do?
The power available to perform work is called real power (kW). Inductive loads such as motors, transformers, and high-intensity lighting introduce reactive power (kVARs) into a power system. The system capacity is rated by the apparent power (kVA) which must be large enough to accommodate both the real power (kW) and reactive power (kVAR). Since reactive power requires system capacity, but performs no work, utilities charge more for it and plants try to keep net kVARs low. High reactive power translates to low power factor.
Power Factor Facts:
- Utilities may charge higher rates or penalties for low power factor or high VARs
- System capacity restrictions cause voltage drops and overheating
- Inductive VARs can be corrected by applying capacitors or active conditioners
How Much Does Poor Power Factor Cost?
Sample Calculation:
Assume the utility adds 1 % of demand charge for each 0.01 below PF of 0.97. Assume your PF averages 0.86 each month and your demand charge is $7000. (0.97 – 0.86) * 100 % = 11 % (11 % x $7000) x 12 months = $9,240 avoidable annual cost.*
* This case study was written in 2005 so based on the 2005 exchange rate from $ to £ it equated to £5,082 back in 2005.
What to Check?
- See if your utility rate plan imposes a charge for reactive demand or power factor
- Find out how the utility measures power factor or VARs. For example, are they looking at peak intervals or averages?
- Identify loads that are causing lagging reactive power and develop a strategy for power factor correction
How Much is OK?
To avoid paying higher utility fees, power factor should be higher than .97. Capacitors or conditioners may be applied on individual loads, at a confluence of several, or at the service entrance to improve power factor.
Note: This varies. Some utilities charge a rate for every percentage point between .85 and .97. Some charge a rate based on the number of VARs you use. Some don't charge at all.
Before and After
The power correction system lived up to expectations. Six screens from the power quality analyser tell the whole story.
SEE THE 6 BEFORE AND AFTER SCREENS FROM THE POWER QUALITY ANALYSER
The change in current is a real testimony to the impact of power factor correction. By correcting the power factor the rms current drawn by the MCC was reduced by 27%. You can see what happens in the power measurements. The power conditioner uses a relatively small amount of power to run. But it counteracts the reactive power, and reduces the apparent power (kVAs) dramatically. You can see the power relationships in the vector diagrams below.
Prior to the installation, the upstream distribution equipment had to carry a lot of reactive current and harmonic current that was sloshing around without doing any real work. Now the system carries only hard-working current to the MCCs.
The power corrector cleaned up the harmonic content, too. Most of the non-linear load was from large motor drives. The 5th harmonic was a big contributor to the overall distortion. Both the amount of the 5th harmonic current and the current THD were cut by more than 50%.
Why Correct Harmonics?
What is harmonics?
Total Harmonic Distortion (THD) is the sum of the contributions of all harmonics. Harmonic distortion is a normal consequence of a power system supplying electronic loads such as computers, business machines, electronic lighting ballasts, and control systems.
What does harmonics do?
Harmonic distortion can cause:
- High current to flow in neutral conductors
- Motors and transformers to run hot, shortening their lives
- Increased susceptibility to voltage sags, potentially causing spurious resets
- Reduced efficiency of transformer or, a larger unit is required to accommodate harmonics
- Audible noise
How much does an incident cost?
The major costs are associated with shortened life of motors and transformers. If the equipment is part of production systems, income may be affected as well.
Sample calculation:
Assume the cost to replace a 100 KVA transformer is $7000 including labour each year. Assume 8 hours of downtime each year with income loss of $6000 per hour. Total Cost: $7000 + (8 x $6000) = $55,000 annually.
* This case study was written in 2005 so based on the 2005 exchange rate from $ to £ it equated to £30,250 back in 2005.
What to check?
Motors, transformers and neutral conductors serving electronic loads.
How much is ok?
Voltage distortion (THD) should be investigated if it is over 5% on any phase. Some current distortion (THD) is normal on any part of the system serving electronic loads. Monitor current levels and temperature at transformers to be sure that they are not overstressed. Neutral current should not exceed the capacity of the neutral conductor.
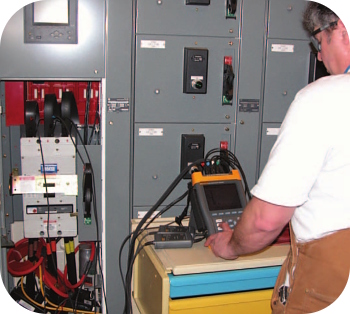
Maintenance Electrical Specialist Mark Newport using a FLUKE 434 Power Quality Analyser to measure, trend, and document the power factor and harmonics correction provided by the plant's new power correction system.
Wastewater plant photo by Ivan Bandura on Unsplash